Toyota is the world’s largest car manufacturer and the most successful car producer in terms of sales, production and customer satisfaction. The company has adapted to changing market conditions by implementing a “kena” or pull system for its car manufacturing. The kena system enables Toyota to keep a very high level of quality control throughout the production process and to reduce costs in areas such as waste disposal and cycle count. Waste disposal of a car is a complex problem because it involves dealing with waste water, solid waste and the pollution of landfills.
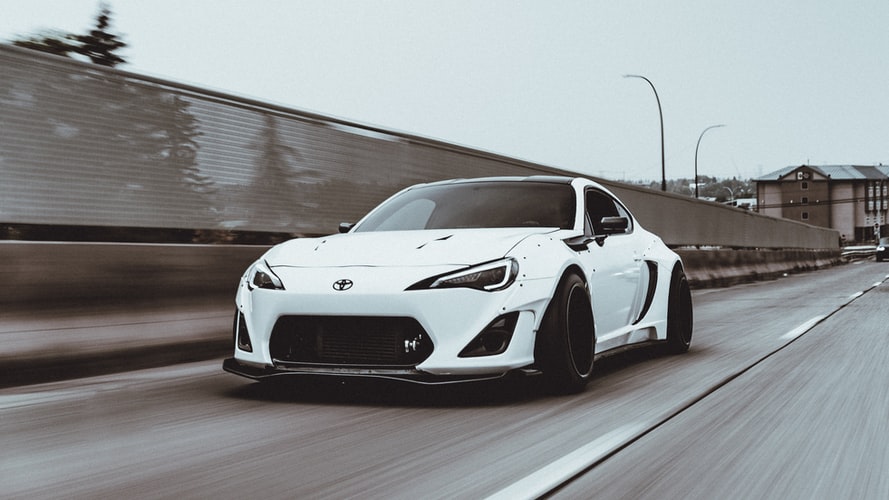
How Successful Has Toyota Been?
Toyota has been successful because of its innovation and lean manufacturing philosophy. The Japanese company started out inkeskin production (using manual labor to mass manufacture) in Toyko in 1947. Today Toyota still mass produces cars in multiple locations under the “lean manufacturing” system. In lean manufacturing, Toyota uses automated processing and other techniques such as lean manufacturing planning, simultaneous production, short lead times and constant engineering supervision. In other words, Toyota takes advantage of the economies of scale that are afforded by using lean manufacturing principles.
A “kena” is a department or level head in a lean production organization. In Toyota, there are seven wastes or aspects involved in any given manufacturing activity. These include plan review, material planning, manufacturing scheduling, material pricing, work instruction and design, production accounting and manufacturing operation and last but not least shipping. These seven wastes must be identified and dealt with in every Toyota car plant. If these aspects are not dealt with on a timely basis, the company runs the risk of being ordered into a recall. And in case of a recall, it would mean lost money for Toyota as well as possible repercussions on their reputation among their customers.
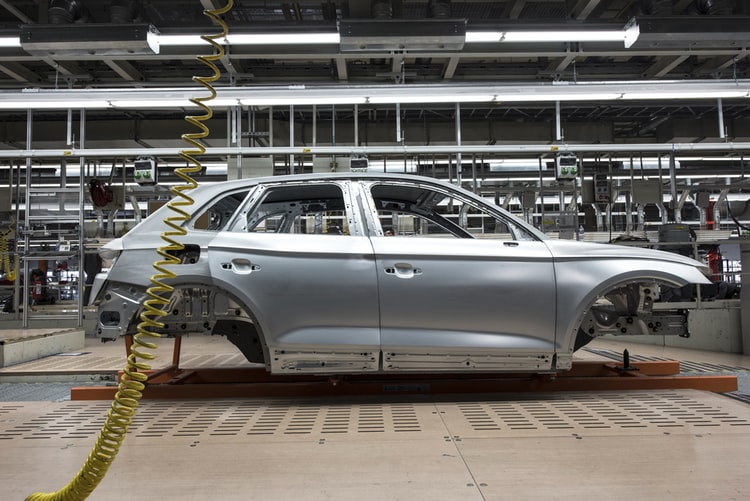
Methods And Techniques Used In Manufacture And Production
Toyota adopted a pull system for its car manufacturing. This is a relatively simple and yet extremely effective car production and waste reduction method. The pull system makes use of a “kena” or member of staff who holds the actual steering wheel. Whenever an action or idea is suggested by a junior employee, the suggested idea is acted upon by the kena and this leads to increased levels of production.
Toyota implemented this new car manufacturing method in May of 1993. Since then, car production has improved considerably. An increase in car production is the result of dealing with the waste issues associated with car production. The overall effect of using a pull system is to reduce waste, shorten cycle times and improve the quality and quantity of car made.
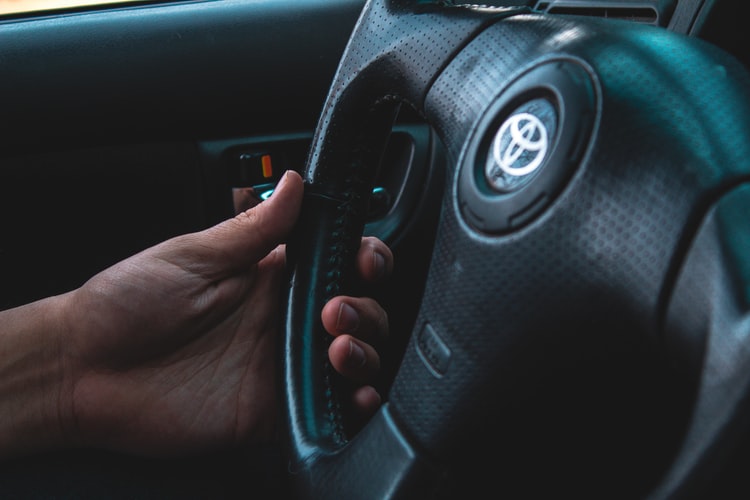
Steps To Success From Within Car Manufacturing
Toyota is a world leader in car manufacturing. Over the years, they have developed a culture where waste is tackled head-on, no matter how trivial. Pulling car manufacturing to the maximum level is only one example of their success in making cars. The company constantly studies new ways of reducing waste so as to produce cars that are better than any competitor in the car manufacturing industry. The result is a product that has been designed and built with speed, efficiency and durability in mind. All of which make the Toyota brand world renowned.
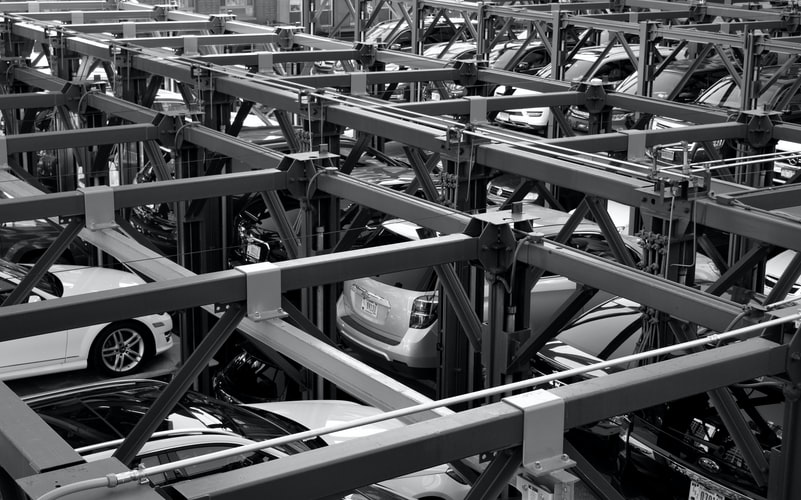